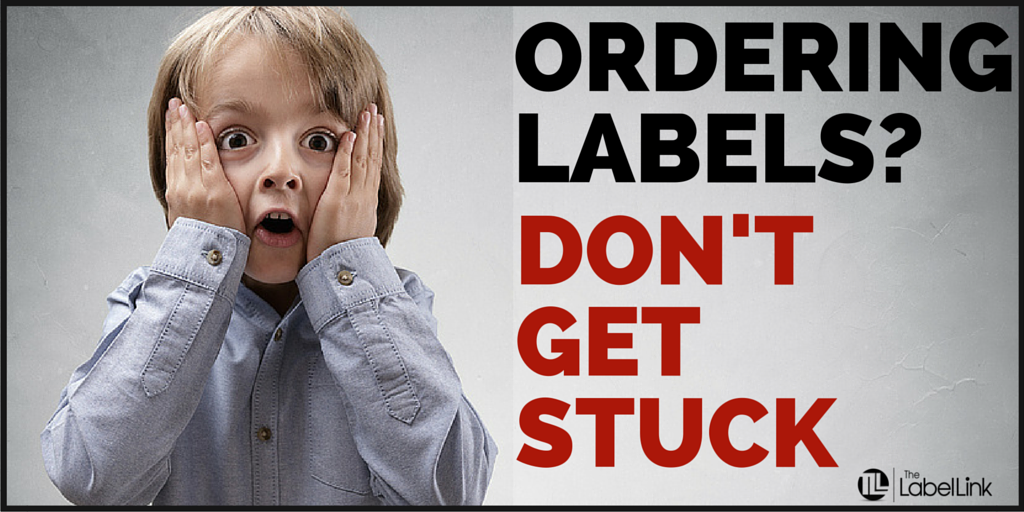
Hate surprises on your label orders? You’re not alone.
Purchasing labels can get confusing, leading to unwelcome surprises. The industry standards known by “everybody” aren’t always clear – especially to people who are new to the world of printing.
Before you place your next order, you want to know exactly what you’re going to get. You don’t want to be caught off guard because something wasn’t discussed or was buried in fine print. Some common questions manufacturers have about the label printing standards include:
- Why didn’t I receive the exact number of labels I ordered?
- What does Price/M mean?
- What is a good way to save on dies?
- What will my labels look like on a roll?
- What are the typical terms and conditions for new customers?
And the list goes on.
I understand how confusing it can get. In this article, I’ll outline the exact label ordering standards to make your order and deliver process stress-free.
Order Quantity Standards: The 10% Overs/Unders Rule
Did you know that even when you order 10,000 labels, your order will be considered complete when 9,000 (or 11,000) labels are printed? This is known as the 10% overs/unders rule.
Printers hate waste. To ensure your printer hits the target order quantity, they must order excess material. That means that if you order 10,000 labels, you could pay for 11,000.
Here’s the good news. Unit costs are often low, so adding materials for an extra 10% of your labels won’t have a significant impact on the cost when ordering a small amount of labels. However, as your order gets higher, such as 500,000 labels, this 10% addition can be substantial.
When you get your order, you might be surprised to find 10% under the amount you ordered. This is still considered a complete order by label industry standards, but for you, it could mean lost money and time.
To ensure this doesn’t happen:
- Order the number of labels you need and specify “no unders” at the time of the quote (which may result in an upcharge);
- Order “exact quantity” so you get the exact number you ordered;
- Order 10% more of the labels you planned on so at the minimum, you get the amount you need (this won’t impact your price point if you’re ordering a lower quantity).
Pro Tip: When ordering a high volume of labels, always request a lower percentage of overs/unders.
Minimums
There are no industry-specific minimum sizes. Still, many traditional flexographic printers maintain a standard minimum of 1,000 labels per order and 500 labels per sku. It varies greatly, so check with your printer for their specific details.
Unit of Measure: Price Per Thousand (or $/M)
Labels are priced per thousand units; not per label.
For example, if you’re ordering 10,000 labels at a cost of $53.00/thousand, you’d expect to pay $530. The price of “each” label is $0.053 (or $53/1,000) but most printers don’t list prices in this manner.
Prices are listed using the Roman numeral system of “M” instead of the Greek kilo system of “K.” Units are shown in the thousands by notating an M at the end of the number. For example, 10,000 will be shown as 10M, not 10K. This standard was put in place before the metric system was used for printing.
Want to impress your friends? Brush up on this example from O’berk bottle company on the $/M before your next trivia night!
Die-Cut Size
There are no industry standards on sizes. Still, you should always request the closest existing tool from your printer to see if what they have on hand will work. This could save you hundreds of dollars!
When calculating the dies, remember your radius corners. The industry standard radius corner is ⅛”. If you don’t specify the radius on your order, this will be the default.
When calculating the size, specify the height x length. Typically, commercial printers use length x height so be careful. This is especially important if you’re automatically applying labels. For more information on this, see our article about how to measure a label.
Space Requirements
Sometimes, you’ll need to leave spacing around your labels. When you do, here are the industry standards for space sizes:
- Spacing between labels on the liner (the carrier of the labels) is ⅛”
- Spacing from the label to the outside edge of the roll is 1/16” on each side
- When you’re automatically applying wrap-around labels, you must have at least ⅛” gap after application; preferably 3/16”.
Label Finishing Requirements
When you’re finishing your label order, here are the industry standard requirements.
- Rolls of 1,000 labels
- Sheets of 500 labels
- A 3” core inside the roll
- Outside diameter of 12”
Materials
Depending on which type of material you use, there are specific label ordering standards.
- Paper: Semi-gloss, perm, or 40# liner
- Coatings: UV gloss or gloss lamination
- Shape: Rectangle, circle or square
Terms
When ordering, most printers will have the following standard terms:
- A 50% deposit (on new orders)/Balance COD (unless credit is established)
- Net 30 day terms (upon approved credit)
- UPS Ground shipping, if not specified
Question: What label order standard has taken you by surprise?
Good printers always ensure you’re aware of these standards and answer your questions. However, many times the above standards are presumed and not addressed directly. If you don’t know what to ask, you can expect to get the above items.
Want to get more information about your label printing? Sign up for our newsletter to receive our latest tips delivered straight to your inbox.